高純鈦濺射靶現在已廣泛應用于半導體裝置制造的金屬鍍工藝中! 日本的日礦材料公司生產高純鈦濺射靶、銅、鉭、鈷、鎢、鎳等高純金屬以及合金靶、鈦硅化物靶等!供給全世界的半導體廠家。高純鈦濺射靶主要是用做鋁配線的擴散阻擋層的氮化鈦膜以及晶體管柵極的鈦硅化物。前者是在濺射中通入氮氣以形成氮化鈦膜! 后者是在硅上形成鈦膜后由熱處理得硅化物膜。
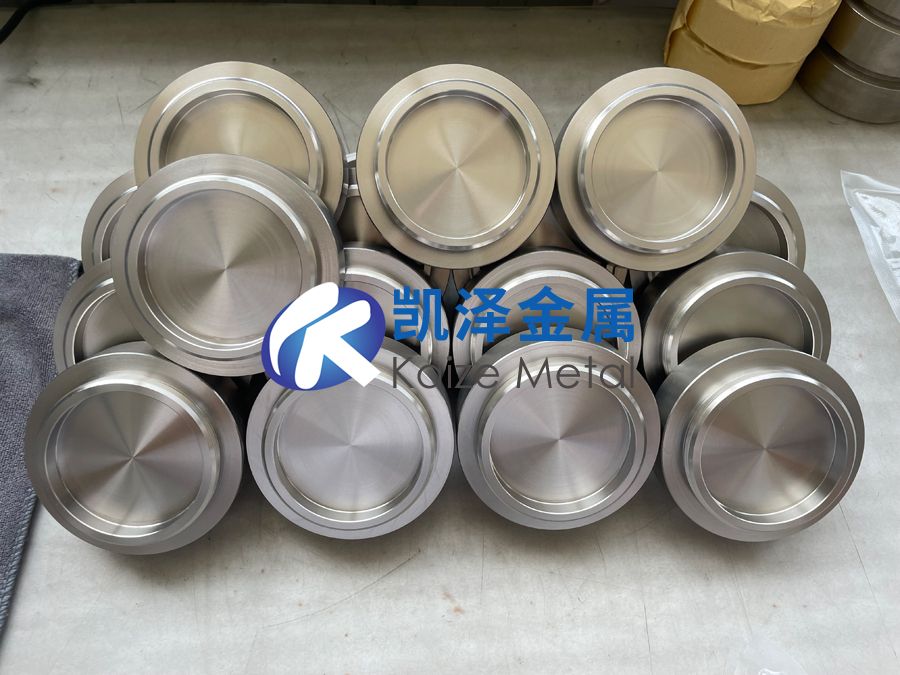
一般靶材在濺射初期特性不穩定,因此要用硅試片進行預濺射!這既耗費時間!降低生產效率,又使硅試片的再生費用增大! 因而需要開發預濺射時間短的靶材。 濺射初期特性不穩定是由于靶材表面物理特性與內部不一致引起的,即靶材在機械加工時其表面形成了加工應變層以及極細小的加工屑的緣故。
對機械加工的鈦靶表面進行了測量和分析,結果表明,表面的平均粗糙度約為2.5μm;掃描電鏡(SEM)觀察發現表面存在許多片狀鈦微塵(加工屑);用X射線衍射(XRD)法來大致推算加工應變層的厚度約為50μm。 因此,為了縮短預濺射時間,必須完全除去表面的加工應變層以及殘存的片狀鈦屑。
日礦材料公司開發了一種新的表面處理方法,稱作sputter Ready(SR)該方法分4 步進行,首先除去機械加工的應變層,然后除去上述工序引入的新的應變層,最后對靶材表面進行鏡面拋光處理。這樣總共要研磨去除約80μm對經過該種表面處理的試樣進行了表面粗糙度測定、SEM觀察、XRD測定及研磨砂布引起的污染的測定。
表面粗糙度的測定結果表明: 平均表面粗糙度約為0.25μm,約為機械加工表面粗糙度的1/10 SEM觀察表面,表面的機械加工痕跡已完全除去,表面存在的片狀鈦微塵。(加工屑)也已完全除去,未有發現研磨的傷痕,XRD測定的(002)面半峰寬比機械加工的小,表明已除去了機械加工的應變層,但比電解加工表面的大,表明機械研磨引入了新的加工應變層,因此,還要對靶材表面進行鏡面拋光處理。 對表面處理的試樣進行洗凈后用輝光放電光譜分析,結果表明,試樣表面的Al、W、Co、Si的含量很低,可以確認其表面已是清潔的表面。
對表面處理的鈦靶材進行實際的濺射試驗評價,硅片直徑為203.2mm,鈦靶直徑為329.692mm,氬氣壓力為661.61Pa,基板與靶的距離為45μm,基板溫度為150℃,用激光照射以檢驗鈦靶表面有無微塵異物, 用OMNI、Map RS-75儀測定鍍膜硅片上49點的比電阻,用以進行膜厚均勻性的評價。結果表明,經SR處理的鈦靶在濺射初期微塵顆粒約為2.3%,而機械加工的鈦靶的濺射膜,其膜厚均勻性在電功率達10KW以上時仍不穩定,這是由于機械加工引起的加工應變層使得在濺射時濺射粒子的出射角度不一致造成的。
近年來,半導體裝置的內部配線材料由鋁改為銅,隨之擴散阻擋層也由鈦靶改用鉭靶,晶體管柵極也由鈦硅化物改用鈷硅化物和鎳硅化物。而上述開發的SR表面處理技術不僅適合于鈦靶,對其它各種靶材的縮短濺射初期的預濺射時間也是有效的手段。
相關鏈接