引言
近年來,計算機輔助設計技術(CAD)的進步,推動了增材制造(AM)(又稱 3D 打印)技術的快速發展。 增材制造技術是一種基于三維數字模型,對產品進行建模分層,采用逐層制造方式將材料結合起來形成產品的工藝,其工藝流程如圖 1 所示[1] 。 目前,增材制造技術被廣泛應用于各個領域(如圖 2),主要成形的材料有鋁合金、鈦合金、鎳基高溫合金以及陶瓷等[2?3] 。 金屬材料增材制造技術依據其成形原理可分為:激光燒結式(SLS)、熔融沉積式 (FDM)、激光熔化式(SLM)、激光熔覆沉積(LCD)和電子束熔化沉積(EBM),其成形工藝對比見表 1[4] 。 常用的激光熔覆技術與選區激光熔化技術原理如圖 3、圖 4 所示[5?6] 。 增材制造所使用的金屬粉末除了需要具備良好的可塑性之外,還必須滿足粉末粒徑細小、含氧量低、粒度分布區間較窄、球形度高、流動性好和松裝密度高等要求。 當前,增材制造能夠應用的金屬粉末材料種類包括模具鋼、鎳合金、鈦合金、鋁合金和青銅合金等。 一般情況下,激光選區熔化成形中所需粉末粒徑在20~45μm,而激光熔覆成型中所需粉末粒徑一般在 90~150 μm[7] 。 目前,等離子旋轉電極法(PREP)、等離子霧化法(PA)和氣霧化法(GA)是增材制造用金屬粉末的主要制備方法,三種方法都可以制備球形或者近球形金屬粉末。
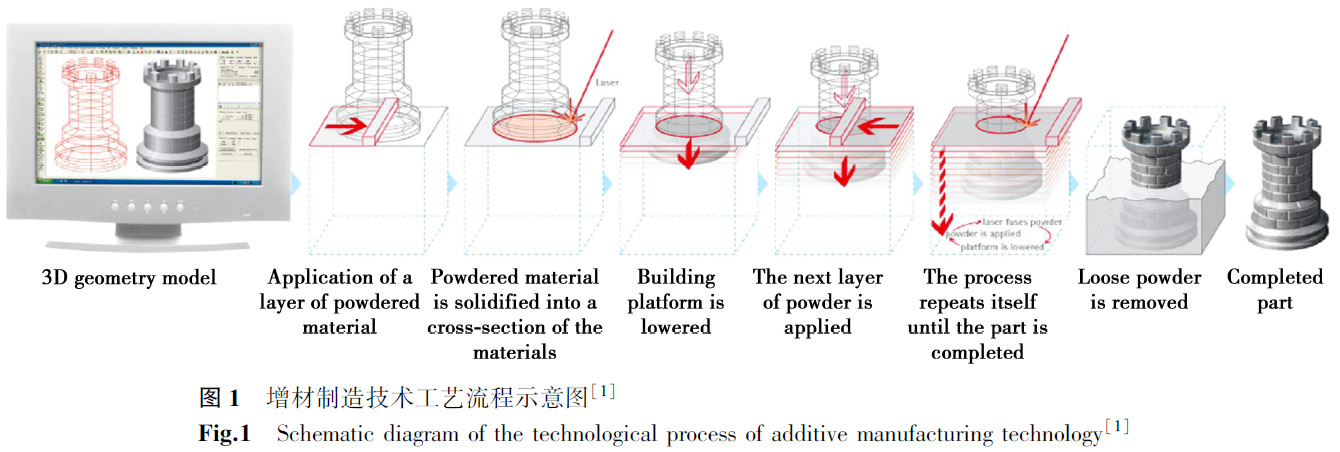
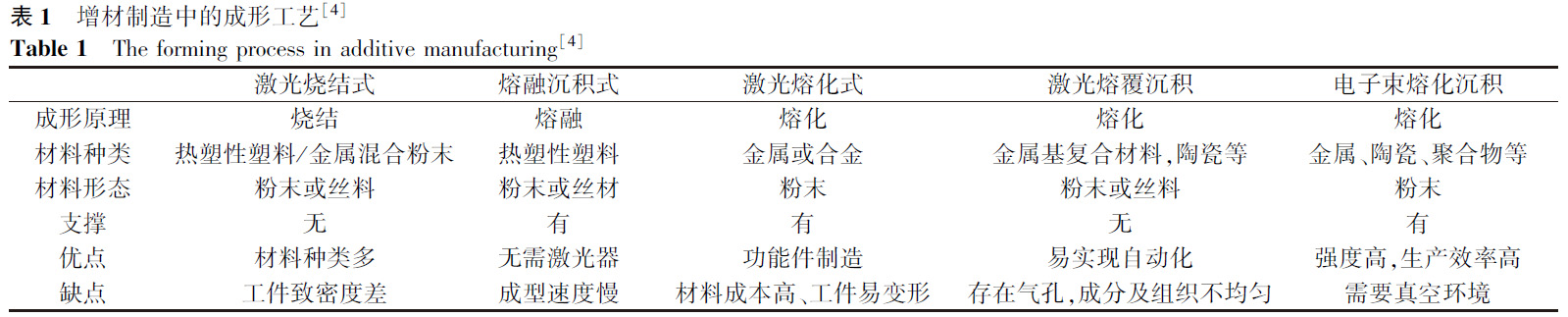
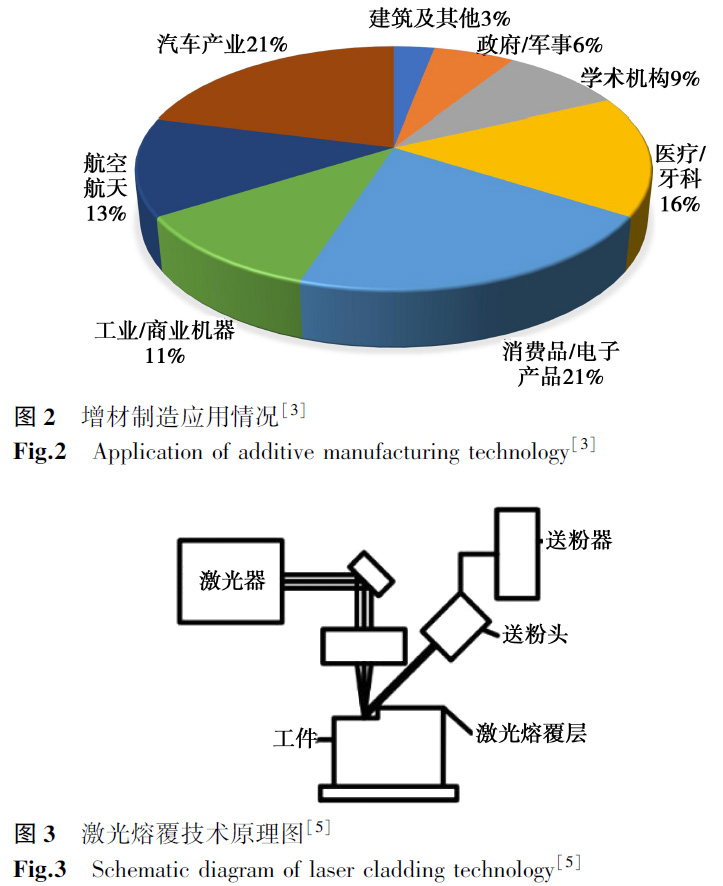
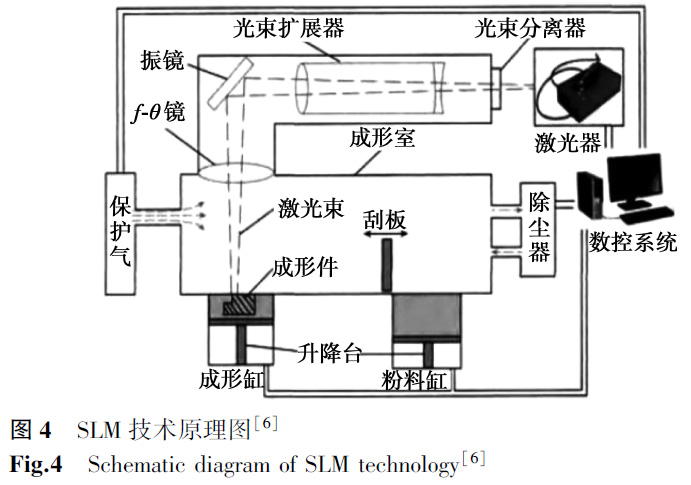
相比傳統制造,增材制造具有以下優勢:(1)節約環保,沒有邊角料,材料利用率高;(2)可生產形狀結構復雜的產品;(3)按生產情況所需,即打即用;(4)生產周期短,效率高。
因此,增材制造技術被廣泛地應用于航空航天、醫療、教育、生活等各個領域,主要體現在機械制造領域。 但是,增材制造技術也存在著以下的問題[8] :(1)大部分工藝采用的原料是粉末,其制備要求較高;(2)材料成型的過程比較難控制;(3)所得成形件的精度不高;(4)增材制造過程中的支撐結構制備技術不成熟;(5) 所應用的軟件編程技術有待進一步提高。
1、鎳基高溫合金研究進展
鎳基高溫合金是一種在高溫條件下(540 ~ 1 000 ℃ 范圍)具有高強度、抗氧化能力好、蠕變強度和持久強度好以及抗燃氣腐蝕能力的材料。 它是基于 Cr20 Ni80 合金發展起來的,為滿足高溫熱強性和氣體介質中的抗氧化和抗腐蝕的要求,加入了大量的強化元素,來保證其優越的高溫性能。 鎳基高溫合金憑借其優異的綜合性能,被廣泛應用于航空航天領域、汽車通訊領域、船舶制造領域等(見圖 5)。 鎳基高溫合金的開發和使用開始于 20 世紀 30 年代末期,是基于飛機對材料的綜合性能提出更高要求的背景下發展起來的,英國于 20 世紀 40 年代初率先生產出 NI75 鎳基合金,后來美國和蘇聯也相繼研制出鎳基高溫合金,中國于 20 世紀 50 年代研制成功。 鎳基合金的發展包括合金成分的改進和生產工藝的創新兩個方面,真空熔煉技術的發展為制備鎳基合金提供了條件。 之后,通過熔模精密鑄造工藝制備了許多具備良好高溫強度的鑄造合金。 鎳基高溫合金種類繁多,已成熟應用于 SLM 工藝的合金材料有 K4202、GH3536、IN738LC、IN625、IN718 五種[9] 。
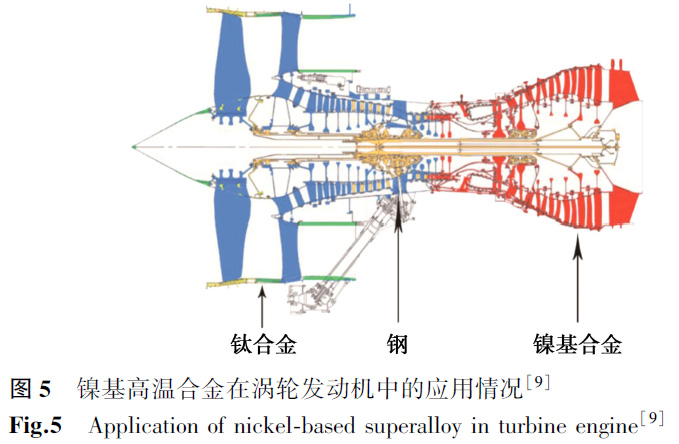
未來,鎳基高溫合金的發展趨向于低成本、高強度、密度小以及抗熱腐蝕性方向。 鎳基高溫合金的發展有以下幾個方面[10] :(1)發展耐腐蝕性能優越的單晶合金;(2)保持組織穩定性,提高材料強度;(3)降低昂貴金屬元素的添加量,節約成本;(4)研究發展密度小的單晶合金。 隨著我國工業化的進步,鎳基高溫合金以其優異的性能在航空領域所占比重越來越大,尤其用于制造發動機受熱部件以及火箭發動機的各種高溫部件。 隨飛機發動機性能要求的提升,對材料的要求也相應提升。 因此,推進耐高溫以及耐腐蝕性能的合金發展對我國航空事業的發展有著重大意義。
2、增材制造鎳基高溫合金研究現狀
激光增材制造對于鎳基高溫合金的制備具有獨特的優勢,如生產周期短、成本低以及可進行功能預設等。 對于航空發動機及燃氣機輪中噴嘴、燃燒室等熱段部件以及航天飛行器等復雜零件的成形制造非常有利[11] 。 近年來激光增材制造鎳基高溫合金受到廣大研究人員的關注,研究熱點主要有以下幾點[11?13] :(1)激光增材制造過程中凝固組織的變化規律;(2)激光增材制造過程中工藝參數與熔池宏觀形態間的關系;(3)激光增材制造過程中殘余應力的分析探究;(4)激光增材制造過程中的缺陷的探究。 國內外的專家對激光增材制造鎳基高溫合金做了大量的研究,以下對激光增材制造的鎳基高溫微觀組織以及力學性能等方面進行介紹。
2.1 微觀組織
2.1.1 3D 打印沉積態的微觀組織
目前,應用增材制造工藝制備鎳基高溫合金較為普遍,最常用的方法主要有 SLM 和 LCD 技術兩種。 增材制造技術制備的鎳基高溫合金與傳統制造所得合金在微觀組織以及
性能上差異較大。 通過不斷調整工藝參數探究增材制造制備的鎳基高溫合金的微觀組織以及缺陷變化,尋求最優化的制造工藝,來提高增材制造鎳基高溫合金的應用性能。
金屬增材制造沉積過程中,高能量激光束熔化金屬粉末,掃描過程中會形成熔池特征。 激光束光斑直徑在微米尺度,故熔池尺寸也在微米等級。 且成形過程中移動速度較快,激光束能量集中,熔池附近溫度梯度高,熔池冷卻很快,晶粒沒有充裕的時間長大。 熔池與金屬粉末、已凝固區以及周圍氣體存在熱傳導、熱對流等,故散熱方向復雜多樣。 因
此,增材制造過程顯微組織的形成極其復雜,與傳統工藝產品的微觀組織差異較為顯著。 增材制造鎳基高溫合金零件沉積態 形 貌 一 般 為 典 型 的 魚 鱗 狀 相 互 搭 接 的 熔 池 形 貌。
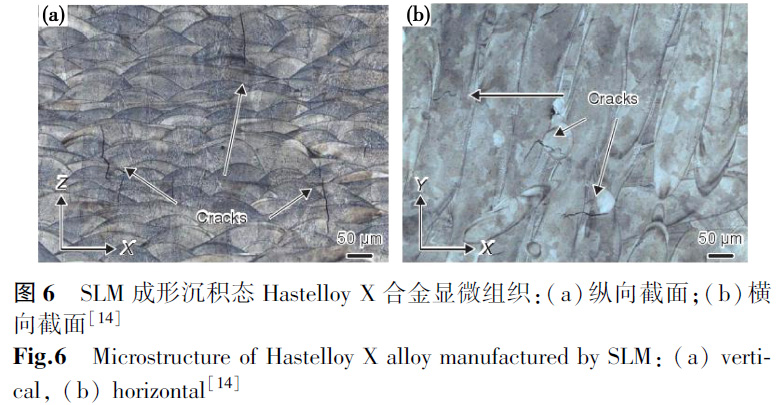
圖 6[14] 為 SLM 工藝制備 Hastelloy X 合金縱向和橫向截面的微觀組織,從圖中可以觀察到沿沉積方向熔池層疊,呈魚鱗狀。 這種魚鱗狀形貌的形成的原因[15] 是:每根熔線截面受激光熔化本道熔線的形貌和相鄰下一道熔線形成過程的影響,下一道熔線成型前,當前熔線的底部呈碗狀,而頂部的形狀受到液態表面張力以及底部熔池熔液的粘附力共同作用,一般呈弧形。 當下一道熔線成型后,依據掃描的方向,前一道熔線的部分形貌因部分重熔而被后一道熔線擦除,擦除部分的多少取決于掃描間距的大小,掃描間距越小,擦除部分越多,最終會形成魚鱗片狀單層結構。
實際應用過程中,晶粒的取向對金屬零件的使用性能有著非常重要的影響。 增材制造鎳基高溫合金零件的晶粒主要包括柱狀晶粒和部分的等軸晶粒。 陳夢洋等[16] 對增材制造的 FGH96 高溫合金成形件進行了顯微組織觀察,發現其組織基本上為柱狀晶組織,接近表面處有細小的等軸晶生成,這種典型的組織在相關文獻中已經得到證實[17] 。 利用 EBSD技術進一步分析發現,當打印的材料厚度不同時,其組織結構也并不相同。 當厚度為 2 mm 時,主要以柱狀晶為主,大部分為立方織構{001}〈100〉;當厚度為 5 mm 時,主要為柱狀晶和等軸晶,柱狀晶區域織構主要是{001}〈120〉和{001}〈230〉,等軸晶織構主要為{113}〈141〉。 增材制造合金組織中柱狀晶和等軸晶的形成過程主要為掃描速度快,殘留于沉積層的熱量來不及擴散出去,前一層對下一層沉積起到了高溫回火的作用。 隨著沉積層厚度的增加,熱量逐漸積累,試樣整體溫度升高,對后一層回火溫度越高,所以后一層的組織以柱狀晶方式生長。 當沉積接近頂層,試樣接觸空氣產生急冷效果,進而導致表面形成了細小的等軸晶。
目前,對于增材制造鎳基高溫合金的研究發現,形成的晶粒尺寸除柱狀晶區外,還存在細晶區和粗糙蜂窩狀晶區,結果如圖 7 所示[18] 。 這種現象是因為隨著激光能量的輸入,粉末熔化形成細小的晶粒,并且掃描過程中出現重熔區,使得高能量輸入區域的亞晶胞狀組織長大成蜂窩狀的粗糙胞狀組織,而另一部分晶粒在負溫度梯度下沿粗糙界面長大成柱狀晶。
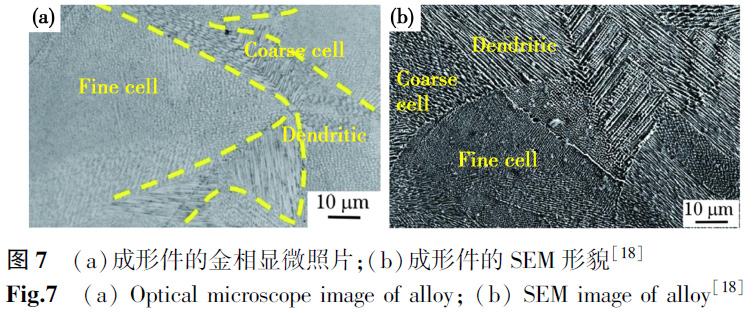
晶體的各向異性是由于沿晶格的不同方向,原子排列的周期性和疏密程度的不同,導致晶體在不同方向的物理化學特性也不同而產生的持征。 晶體的各向異性具體表現在不同方向上的彈性模量、硬度、屈服強度等的差異。 增材制造技術因其本身工藝的特點,晶體的各向異性特征也非常顯著。 Choi等[19] 利用 SLM 技術制備了 IN718 試樣,利用掃描電鏡對試樣的 XZ 平面微觀組織進行分析,發現熔池中間為柱狀晶粒,柱狀晶粒的生長方向與熔池冷卻的方向基本相同,這與熔池凝固過程中的熱流方向和凝固冷卻溫度梯度有關。 熔池邊緣存在等軸晶粒,且晶體取向具有多種,其原因是[9] :其一,打印過程中熔池邊緣位置發生重熔,導致晶粒生長方向隨熱流方向的變化發生改變;其二,熔池邊緣雜質富集,使得晶粒生長為異向的等軸晶小顆粒。
此外,一些學者對增材制造合金的顯微組織進行分析時,在層與層之間的組織中還觀察到層帶結構,如圖 8 所示[20] 。有研究認為成形件底部形成的層帶組織是在高溫度梯度及低凝固速度下平界面凝固生長的結果,成形件中部的層帶結構則是平界面生長受到擾動失穩所導致的[21]。
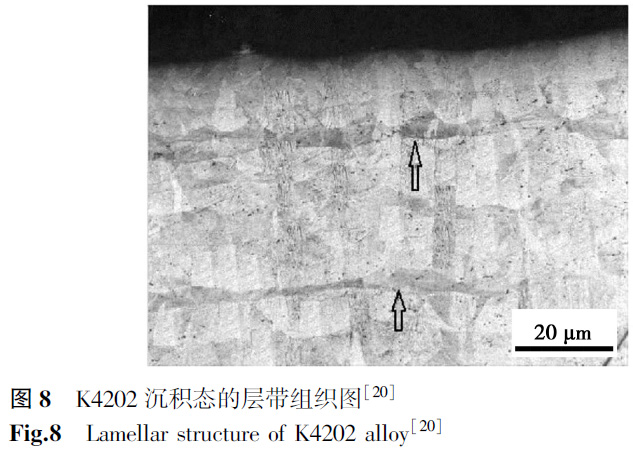
增材制造制備鎳基高溫合金過程中冷卻速度很快,最初形成 γ 枝晶干,溶質元素不斷進入枝晶間的液相中,出現成分過冷與枝晶偏析現象,故枝晶間會產生許多低熔點共晶相。
通常情況下,共晶反應首先發生,形成一次碳化物 MC,凝固最后階段發生 L→γ+Laves 共晶反應,生成大量的 γ/ Laves 共晶。在增材制造過程中,復雜的熱循環會對已沉積層產生熱處理效應,造成共晶產物進一步發生固態相變,析出碳化物以及 δ相等。 呂豪等[22] 對 10 mm/ s 的沉積速度下的 GH4099 合金微觀組織進行了觀察,并對 GH4099 合金沉積態的析出相進行了分析,發現了枝晶之間存在明顯的白亮色相,如圖 9 所示。 利用能譜儀對其進行研究,結果表明,白亮色的相為 γ?γ′共晶相,是 Al 和 Ti 元素在枝晶間產生了明顯的偏析所造成的。
Chlebus 等[23] 對 SLM 技術制備的 IN718 試樣的微觀相分布進行分析時,發現了脆性 δ?Ni3Nb 相和 Laves 相,以及在枝晶結構間離散分布的溶質元素。 此現象出現在多熔道的重熔區域或凝固層的層間重疊區域,主要是由于 Nb 和 Mo 元素在熔池固化的過程中會發生微觀偏聚而形成的,這在一定程度上會造成成形件的殘余應力,進而影響成形件的性能。 Brynk 等[24]向 IN718 合金粉末中添加了不同質量分數的 Re 金屬元素,利用透射電子顯微鏡分析了增材制造所得成形件的微觀組織,結果如圖 10 所示。 他們發現添加適量的 Re 能使 IN718 零件經熱處理后的樹枝狀晶粒更細,但過量會導致有害相 Laves 相和碳化物的增加,在難溶部分的 Re 附近形成許多位錯。
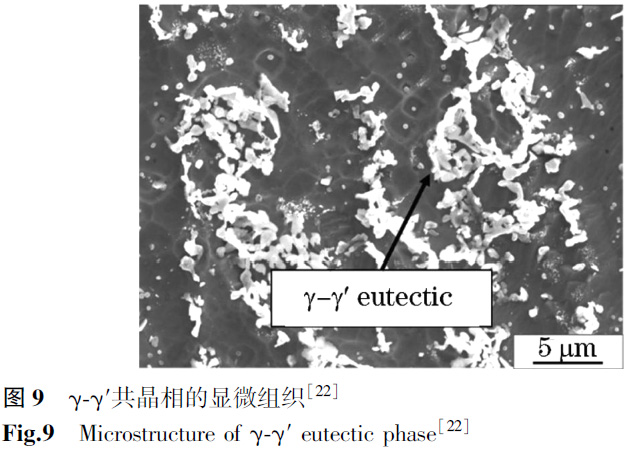
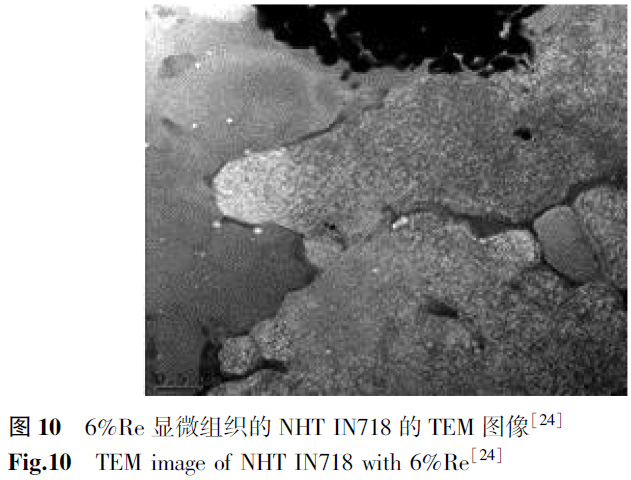
傳統鑄造工藝成形的鎳基高溫合金組織形貌以粗大的枝狀晶狀結構為主,需要通過鍛壓消除顆粒晶界、壓碎枝晶,使得晶粒細化為等軸晶結構達到 SLM 凈成形合金晶粒大小水
平。 增材制造鎳基高溫合金成形件的組織,其形貌為典型的魚鱗狀相互搭接的熔池形貌,晶粒以具有顯著外延性特征的柱狀晶和等軸晶為主,組織中也存在一些偏析所致的脆性
δ?Ni3Nb 相和 Laves 相,這些相的存在降低了成形件的性能。
2.1.2 后處理的組織特征
為了減少或消除增材制造后零件的微觀和宏觀缺陷,提高其綜合性能,進行后處理是很有必要的。 目前,普遍應用的后處理方法主要有熱等靜壓處理(HIP)、固溶處理(ST)和時效處理(AT)。 一般情況下,可結合兩種或兩種以上的處理方法對材料微觀組織進行改善。 對于增材制造所得試樣,選擇合理的后處理工藝能夠極大地改善合金的組織,進一步提高成形件的性能。
熱等靜壓處理的基本原理是以氣體或液體作為壓力介質,使材料在加熱過程中經受各向均衡的壓力,借助于高溫與高壓的共同作用促進材料致密化和元素擴散。 熱等靜壓技術
最顯著的特點是可使處理后的材料仍保持細晶粒的晶體結構。
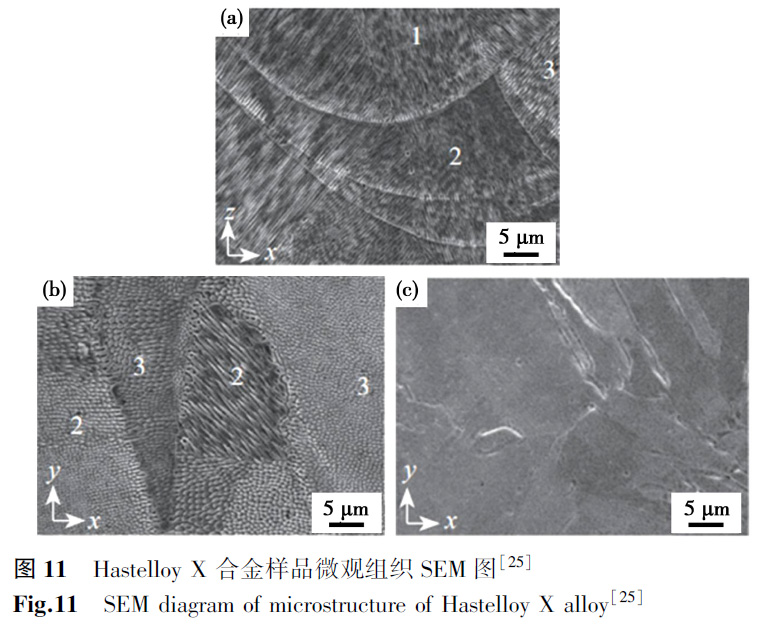
經過熱等靜壓處理后,熔池邊界消失,微觀組織中枝狀晶發生溶解并呈現均勻化,形成等軸晶,如圖 11 所示[25] 。 李雅莉等[26] 對SLM 制備的 Hastelloy X 合金試樣經過熱等靜壓(1 175 ℃,150 MPa,1 h,爐冷)處理后的微觀組織進行了觀測。 研究發現經過熱等靜壓后,熔池形貌消失,裂紋愈合。 同時微觀組織演變為等軸晶,且晶界及晶內溶質元素擴散并聚合,形成了較多的析出物。 張永志等[15] 對 SLM 制備哈氏合金試樣做了熱處理+熱等靜壓處理,研究了橫向和縱向截面的晶粒形態,發現縱向截面中部分晶粒為柱狀晶態,而橫向截面中晶粒基本為等軸晶組織,且橫向和縱向截面存在一定量的細晶區,這是因為在熱等靜壓再結晶過程中,晶粒之間或晶粒與周圍粗晶的取向差異較大,部分細晶不能充分合并長大,導致熱等靜壓后仍存在少量相對較細的晶粒。
固溶處理是將合金加熱到合理的溫度范圍之內,促進溶質原子充分溶解于固溶體之中,進而使得固溶體產生畸變,增大位錯運動阻力,使得合金得到強化。 呂豪等[22] 對激光增材制造 GH4099 合金沉積態試樣進行了固溶處理(1 120 ℃,2 h),研究表明,在固溶處理過程中發生了明顯的再結晶,柱狀晶內部的枝晶形貌消失,轉變為細小的等軸晶組織,且在等軸晶內部存在許多孿晶界。 利用掃描電鏡進一步觀察,發現枝 晶 間 的 初 生 相 發 生 了 明 顯 的 回 溶 反 應,相 的 尺 寸 從10 μm下降到了 200 nm 左右,如圖 12 所示。 這是由于在凝固過程中 Al 和 Ti 等元素偏析到枝晶間形成尺寸較大的初生相,導致沉積態組織中存在微觀偏析現象,形成了枝晶亞結構;而高溫固溶過程也是一個均質化的過程,可以明顯地消除組織中的偏析,使初生相發生回溶,尺寸有所降低,而且 Al和 Ti 等元素在經過固溶處理后充分固溶在 γ 基體中,這使得
存在于沉積態中的枝晶亞結構也會消失。
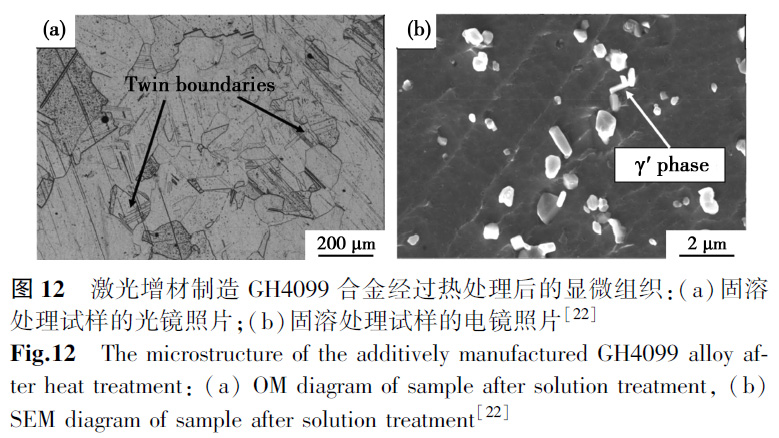
時效處理主要是經時效處理使得飽和固溶體中的合金元素彌散析出在合金基體中,從而形成部分體積較小的溶質原子富集區,進而形成沉淀相,此沉淀相能有效阻止位錯和晶界的運動,改善組織,對合金起到強化作用。 然而,單一的時效處理對組織的改善并不理想,目前應用較為廣泛的是固溶+時效處理方法。 鄧曉陽等[27] 對 SLM 工藝制備的 IN718合金進行了固溶+雙級時效處理(940 ℃×1 h,空冷+720 ℃ ×8 h,56 ℃ / h 爐冷到 620 ℃后保溫 8 h),發現處理后合金在晶內和晶界析出了短棒狀和針狀兩種不同形貌的相,利用 EDS分析發現這兩種相均為 δ 相。 合金中晶界短棒狀 δ 析出相在固溶過程中析出,而晶內針狀 δ 析出相在時效過程中析出。 利用 TEM 與電子衍射對試樣進一步觀察分析,結果如圖 13 所示,發現還存在圓盤狀 γ″相和黑點狀 γ′相,這些析出相強化了合金的性能。
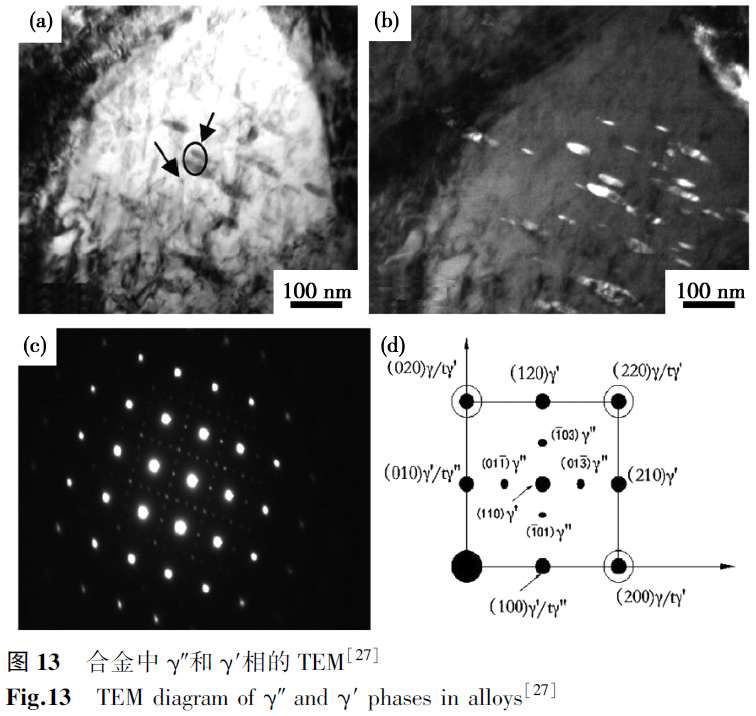
黃文普等[28] 利用 SLM 技術制備了 K4202 合金并進行了固溶+時效處理(1 125 ℃保溫 4 h,空冷至 825 ℃保溫 5 h 再空冷至室溫), 結果表明成形態組織主要為 γ 相, 經固溶+時效和時效處理后,γ′相大量析出。 通過 XRD 對不同后處理狀態下的試樣進行分析發現,試樣中均存在 CrNi、Ni3(Al,Ti)、
Cr2Ni3、Ni17 W3 以及 MoNi4 這幾種物相。 其中基體 γ 相為CrNi,構成 Ni?Cr 基固溶體;γ′相為 Ni3 (Al,Ti);而 Cr2Ni3、Ni17W3和 MoNi4 為合金中的屬間化合物。
經過后處理之后,增材制造所得零件的組織呈現均勻化,熔池邊界消失,晶粒轉變成細小的等軸晶,組織中含有較多不同形貌的 δ 析出相,晶粒的長大被抑制,固溶+時效處理
后,γ′相和 γ″相的析出強化了合金的性能,脆性 Laves 相得到了完全溶解,且 MC 碳化物增加,后處理后組織的變化使得成形件的綜合性能得到充分改善,滿足了復雜條件下樣件應用標準。
2.2 力學性能
力學性能是鎳基高溫合金的一個應用的重要指標,包括強度、延伸率及硬度等。 表2簡要概述了通過不同材料和工藝所獲得的最高可實現的力學性能[29] 。 XY 是指平行于構建平臺構建的拉伸試樣,而 Z 是指垂直于構建平臺構建的拉伸試樣。 在參考平面的橫截面上測試樣品的硬度。 由 SLM制造的鎳基高溫合金零件經后處理后其力學性能得到了極大的改善,表 3 簡要概括了 SLM 成形的各種鎳基高溫合金經后處理后的力學性能。
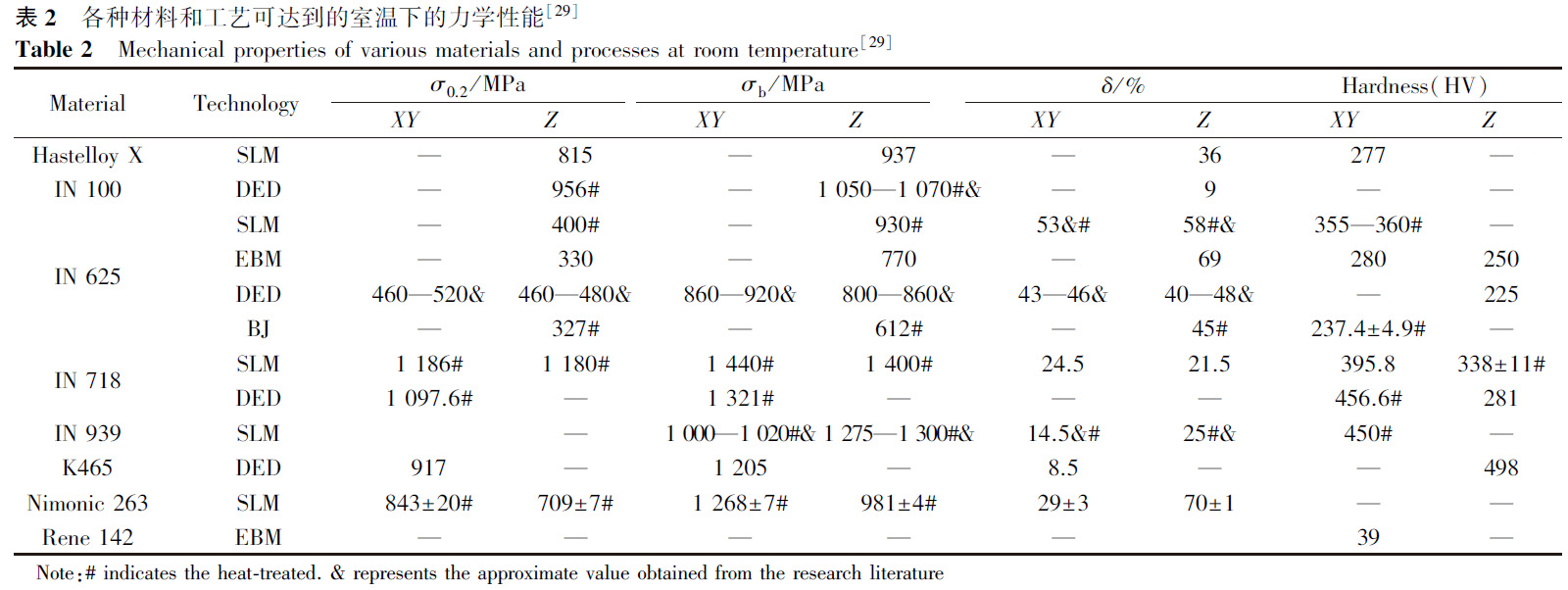
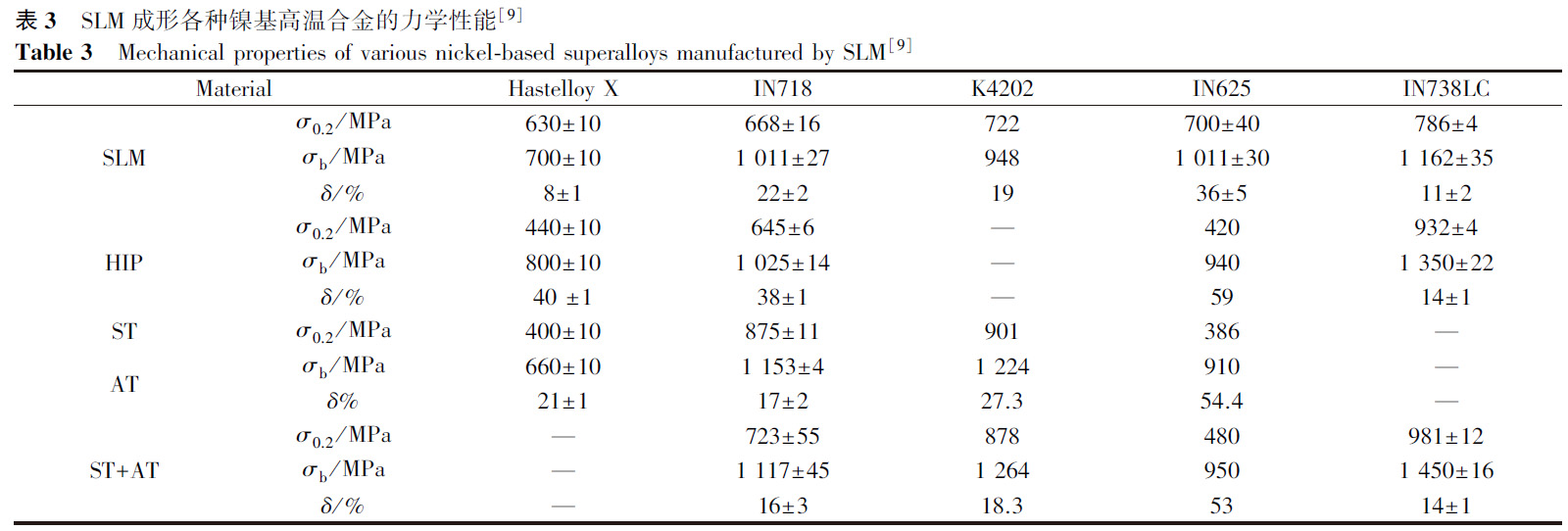
2.2.1 顯微硬度
硬度通常定義為材料抵御硬且尖銳的物體所施加的壓力而產生永久壓痕的能力。 材料的硬度是材料重要的力學性能之一。 不同于拉伸性能的各向異性,增材制造制備的試樣在沉積方向或垂直于沉積方向上的硬度差異比較小。 趙衛衛等[30] 對激光立體成形 IN718 沉積態的顯微硬度做了測試。 圖 14 為顯微硬度沿沉積方向的變化情況,可以發現沿沉積方向,從底部到表層硬度分布較為均勻。
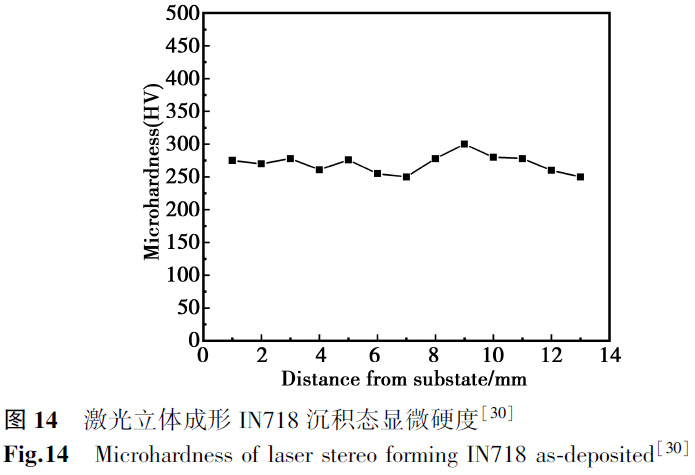
增材制造制備的試樣存在各種類型的缺陷,會對沉積態的硬度造成不同程度的影響。 因此,選擇合適的后處理工藝能夠進一步提高試樣的硬度。 黃文普等[28] 對 SLM 制備的K4202 合金,在沉積態,固溶+時效(1 125 ℃ /4 h,空冷至 825 ℃,保溫 5 h 再空冷至室溫)和時效處理(825 ℃ /5 h,然后空冷至室溫)三組試樣的顯微硬度進行了測試,結果如圖 15 所示。 研究發現,熱處理后的 K4202 試樣的硬度明顯高于沉積態,且時效處理的硬度略高于固溶+時效處理的試樣。 其原因是在熱處理過程中合金中的 γ′相從過飽和的 γ 相中析出,γ′相有效地提高了試樣的顯微硬度。 而固溶+時效過程中再結晶的發生使得晶格畸變和位錯減少,晶粒發生長大,因此固溶+時效處理后試樣的顯微硬度略低于時效處理的試樣,文獻[31]也證明了這一點。
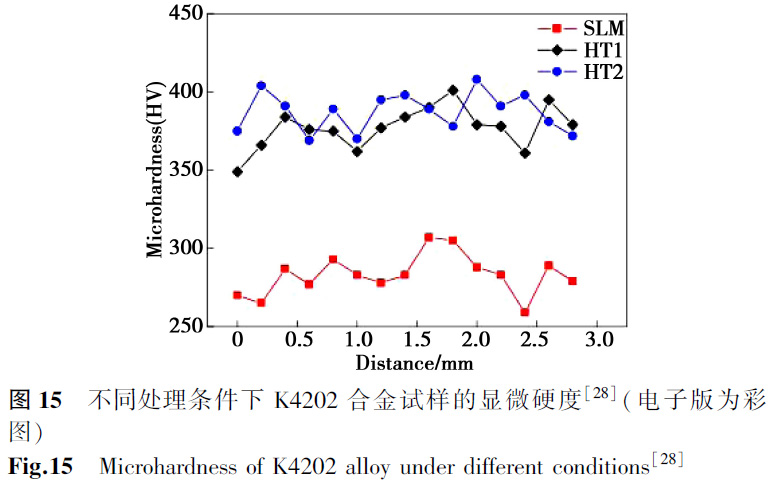
2.2.2 拉伸性能
增材制造鎳基高溫合金相比于傳統的鑄態或鍛態,其顯微組織有著很大的差異, 因而材料的力學性能也不同。 大量研究表明,增材制造技術制備的試樣拉伸性能優于傳統的鑄
造合金。 如表 4 所示,為 SLM 制備的 K4202 試樣的拉伸性能測試結果,結果表明 K4202 合金 SLM 成形態試樣的拉伸強度和塑性明顯優于傳統鑄造合金。
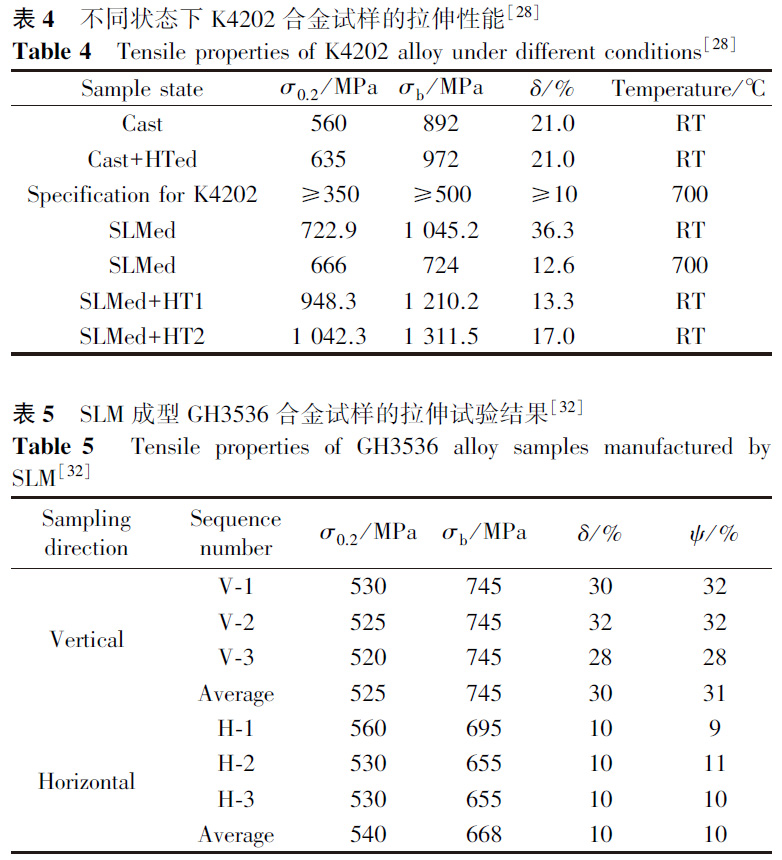
由于增材制造工藝本身的特點,所制備的合金材料顯微組織存在著各向異性,其不同方向的拉伸性能也有所不同。 劉凱等[32] 對 SLM 成形的 GH3536 試樣以 1 mm/ min 的速率在常溫下進行了橫向與縱向拉伸實驗(結果如表 5 所示),研究發現縱向試樣的拉伸性能優于橫向,試樣性能存在各向異性。 通過對增材制造試樣顯微組織形貌的分析可知,縱向試樣的魚鱗狀熔池堆疊層數多于橫向,縱向試樣同層的條狀熔池延伸距離比橫向試樣短,而橫向和縱向顯微組織之間的差異性,是造成試樣縱向和橫向拉伸性能差別的主要原因。
前已述及,因增材制造加工過程中冷卻速率極快,沉積態的晶粒以具有顯著外延性特征的柱狀晶和等軸晶為主,組織中存在偏析所致的脆性 δ?Ni3Nb 相和 Laves 相。 此外,合金內部存在的微裂痕和宏觀方面試樣的殘余內應力等因素,致使合金性能較低,選用合理的熱處理工藝能夠進一步提高材料的性能。 固溶處理、時效處理等能夠改善合金組織,對合金拉伸性能有著不同程度的提高。 左蔚等[33] 研究了三種熱處理條件(固溶、固溶+時效、直接時效)下 SLM 成形 K4202高溫合金拉伸性能,如表 6 所示。 研究發現直接時效熱處理可以獲得優于傳統固溶+時效熱處理制得的室溫拉伸性能,熱處理后抗拉強度達 1 320.6 MPa,比沉積態提高了約 43%。
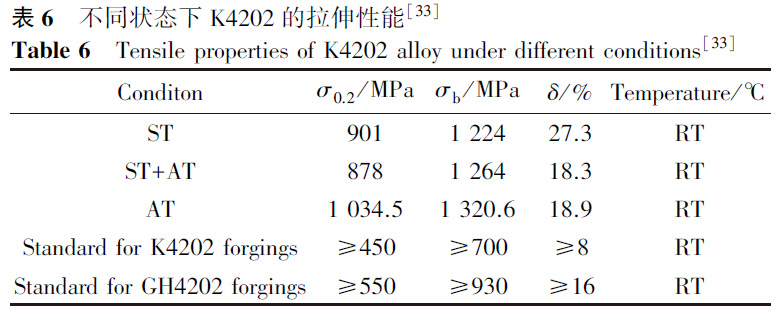
時效處理后試樣拉伸性能較高是因為時效處理后試樣晶粒的尺寸和形貌相對于沉積態變化不大,保留了大量的位錯和晶界,阻礙了位錯和滑移,使其強度得到提高。
通過分析不同的研究發現,相比于沉積態的力學性能,經過不同條件下熱處理后的成形件各項力學性能(屈服強度、抗拉強度、硬度等)均能達到或超過鍛件的標準,強度相比于沉積態零件有不同程度的提高。 相比于直接沉積的成形件,經過后處理后零件的綜合性能有了較大的提升,可以滿足不同領域的應用要求。
3、 現存難點
3.1 殘余應力
殘余應力的定義是材料內部處于平 衡 狀 態 的 靜 態 應力[34] 。 在增材制造過程中,局部快熱或者快冷會產生較大的溫度梯度,很容易形成熱應力殘留在成形件內部。 在特定的條件下殘余應力釋放時,會導致材料產生裂紋,影響材料的綜合性能。 殘余應力的產生因素主要有塑性變形、溫度梯度和固態相變,通常殘余應力的產生綜合了這幾種因素。 激光成形加熱與冷卻速度都極快,在激光增材制造加熱過程中,不同位置溫度不同,熔化不同步,冷卻過程中凝固不同步,使得不同位置的膨脹與收縮具有不一致性,從而產生熱應力。
在激光增材制造成形過程中出現或是在成形完成后馬上出現的缺陷,主要與熱應力有關[35] 。 金屬激光增材制造過程中,應力的產生和演變規律與焊接過程相似,但由于激光增材多層堆積過程中各種條件的差異會使冷卻過程不同,熱過程差異造成應力演化、分布更加復雜,使得增材制造在逐層處理過程引入的殘余應力既復雜又比較大。 通常,增材制造制備的成形件內部并不希望存在殘余應力,因為它會降低成形件的疲勞性能與拉伸性能,最終導致成形件產生幾何變形[36] 和裂紋。
目前,對控制和減少增材制造制備成形件中的殘余應力方面已經做了大量的研究[37?39] 。 圖 16[40] 為不同的殘余應力測試技術對應的測試深度和分辨率。 對于高溫合金盤鍛件,需要測試分析距表層 10 mm 甚至更深的內部殘余應力,分辨率要求為 mm 級,因此主要方法包括中子衍射法(Neutron dif?fraction)、 輪 廓 法 ( Contour method)、 深 孔 法 ( Deep?holedrilling)和超聲法(Ultrasonic)。
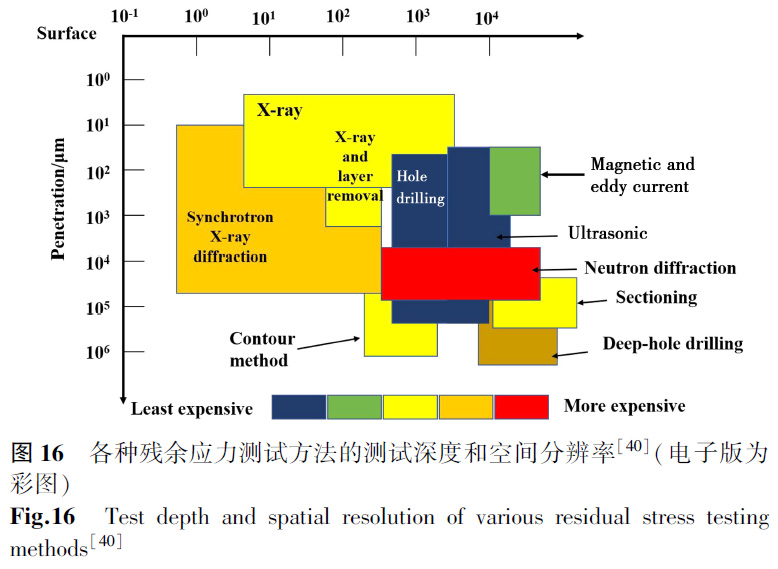
因此,殘余應力的控制與消除決定著激光增材制造成形件質量的優劣。 增材制造主要分為預熱、沉積、后處理三個部分,殘余應力的形成與這幾個過程都存在一定的關系。 通
常,對基板在 150~400 ℃進行預熱可以減少成形件中的殘余應力[41] 。 沉積部分主要是工藝參數的選擇,合理的工藝參數能夠有效地減少成形件的殘余應力[42] 。 近年來科研專家還提出了許多后處理工藝方法以減少殘余應力。 通過熱處理來降低材料殘余應力的方法有熱等靜壓法、退火與固溶時效處理方式。 楊啟云等[43] 測試了選區激光熔化制備 IN625 合金退火(1 140 ℃,2 h)前后的表面殘余應力,發現殘余應力由退火前的398MPa 減小到242MPa,降低了39.2%。 除此
之外,目前常用的有效調控方法還有以下幾種:選擇適當沉積方式;采用與打印材料同材質基材,減小熱導率和熱膨脹系數差而產生的殘余應力;采用機械約束,對成形過程中產
生的翹曲變形進行嚴格控制等。 目前對增材制造中殘余應力的演化規律的認識還存在不足,需要進一步探索更加簡便、高效的處理方法以降低成形件中的殘余應力。
3.2 孔隙
孔隙現象在增材制造成形件中普遍存在,它對成形件的綜合性能有著極其重要的影響[34] 。 孔隙是在材料成形過程之中形成的,熔池內的氣體在材料快速熔化和凝固時因來不及排出而殘留于成形件內形成氣孔,其形狀通常為規則的球形且尺寸較小[44] 。 除此之外,霧化制備粉體材料時內部會不可避免地混入少量的保護氣體[45] 。 在增材制造過程中,粉末熔化使得氣體釋放,若來不及排出則會在成形件內部形成氣孔從而產生孔隙現象。 成形件內的氣孔、裂紋與應力等都對孔隙的形成有一定影響。
目前,針對孔隙現象許多科研專家也提出了同的控制方法。 研究發現,實驗前對基板進行預熱可以減小與熔池之間的溫度梯度,降低熔池的冷卻速度使氣體能夠排除,以達到
減小成形件孔隙度的目的[46] 。 在增材制造過程中,選擇合理的工藝參數對于減少成形件的孔隙度也有極其重要的作用。
此外,采用熱等靜壓對成形件進行后處理,也能減少成形件的孔隙度。 Li 等[47] 對 SLM 制備的哈氏合金做了熱等靜壓處理,結果證明熱等靜壓能夠有效地減少 SLM 成形件中的微裂紋和孔隙等缺陷,Tomus 等[25] 的研究結果也證明了這一點。
未來,對于孔隙率的控制仍需要進一步研究,對孔隙的處理方法需要進行針對性的探究。
3.3 微觀結構的各向異性
一般而言,增材制造技術制備的成形件為柱狀晶結構,且晶粒穿過多個熔覆層向上延伸。 較快的凝固速度以及垂直于基材方向的熱損失使得晶粒在粉床中外延生長。 在選區激光增材制造制備的構件中可以觀察到一些可變性的結構,這是通過使用棋盤式掃描策略導致形成嵌入在主要柱狀晶區域中的近等軸晶區域[48] 。 更重要的是,由于該工藝的反
復加熱性質,顯微組織在幾十微米尺度上也表現出不均勻性,這表現在所見的“魚鱗”形貌和晶粒結構或偏析上的不均勻性[17,49] 。 晶粒結構中的各向異性本身不是問題,但是我們期望可以通過控制晶粒的各向異性來獲得某些特定的力學性能,比如定向澆鑄(Directionally cast, DS)獲得結構的方向性。 通過調控工藝參數進而實現對晶粒尺寸和晶體取向的控制,增材制造技術在這方面具有很大的潛力。 但目前關于這方面的研究還非常少,其潛力還尚未被充分發掘,需要進一研究。
與微觀結構相關的另一個難點是結構中快速凝固副產物的亞穩態性質。 大多數鎳基高溫合金增材制造成形件的結構要么表現出一定程度的枝晶間偏析,要么顯現出其它不希望出現的凝固誘導相(如 Laves 相)[50] 。 因此,通常需要后處理來修復增材制造工藝引起的缺陷。 除了固溶和時效熱處理外,還可以產生一定尺寸和比例的沉淀物來提高材料的高溫特性。 然而,這些后處理操作會進一步增加增材制造工藝的成本,降低它們的吸引力。
4、結語
本文簡述了激光增材制造的各種技術以及鎳基高溫合金的研究進展,綜述了增材制造鎳基高溫合金成形件后處理前后的組織特征以及力學性能。
本文闡述了增材制造鎳基高溫合金成形件存在的缺陷及其形成的機理,概括了目前研究中針對這些缺陷所提出的解決方案,為后續的研究提供參考。
參考文獻
【1】Liu K, Sun H J, Wang J, et al. Advanced Ceramics, 2017, 38(4), 286(in Chinese). 劉凱, 孫華君, 王江, 等. 現代技術陶瓷 , 2017, 38(4), 286.
【2】 Zhou R Y,Shuai M B, Jiang C. Materials Reports A:Review Papers,2016, 30(1), 67(in Chinese). 周汝垚, 帥茂兵, 蔣馳. 材料導報:綜述篇 , 2016, 30(1), 67.
【3】Liao W J, Hu J. The Magazine on Equipment Machinery, 2015(1), 1(in Chinese). 廖文俊, 胡捷.裝備機械 , 2015(1), 1.
【4】Liao W J, Fan E X, Fu C. Materials for Mechanical Engineering, 2018,42(7), 16 (in Chinese). 廖文俊, 樊恩想, 付超.機械工程材料 , 2018, 42(7), 16.
【5】Hu Z N, Zhang Y T, Wang N N. Shandong Coal Science and Technolo?gy, 2014(8), 95 (in Chinese). 胡振南, 張玉堂, 王娜娜.山東煤炭科技 , 2014(8), 95.
【6】Lan F, Liang Y J, Huang B B. Equipment Manufacturing Technology,2018(5), 43(in Chinese). 蘭芳, 梁艷娟, 黃斌斌.裝備制造技術 , 2018(5), 43.
【7】Le G M, Li Q, Dong X F, et al. Rare Metal Materials and Engineering,2017, 46(4), 1162(in Chinese). 樂國敏, 李強, 董鮮峰, 等. 稀有金屬材料與工程 , 2017, 46(4),1162.
【8】Yao F L. Mechanical Management and Development, 2019(8), 116(inChinese). 姚福龍.機械管理開發 , 2019(8), 116.
【9】 Wang D, Qian Z Y, Dou W H, et al. Aeronautical Manufacturing Tech?nology, 2018, 61(10), 49 (in Chinese). 王迪, 錢澤宇, 竇文豪, 等.航空制造技術 , 2018, 61(10), 49.
【10】Tang Z J, Guo T M, Fu Y, et al. Metal World, 2014, 1(4), 36 (inChinese). 唐中杰, 郭鐵明, 付迎, 等.金屬世界 , 2014, 1(4), 36.
【11】Wu K, Zhang J L, Wu B, et al. Journal of Iron & Steel Research, 2017,
29(12), 953.
【12】Gan Z, Liu H, Li S, et al. International Journal of Heat and Mass Trans?fer, 2017, 111, 709.
【13】Seidel A, Finaske T, Straubel A, et al. Metallurgical and MaterialsTransactions: A, 2018, 49(9), 3812.
【14】Zhang Y Z, Hou H P, Peng S, et al. Journal of Aeronautical Materials,2018, 38(6), 50 (in Chinese). 張永志, 侯慧鵬, 彭霜, 等.航空材料學報 , 2018, 38(6), 50.
【15】Wu W H, Yang Y Q, Mao G S. Manufacturing Technology & MachineTool, 2014(4), 46 (in Chinese). 吳偉輝, 楊永強, 毛桂生.制造技術與機床 , 2014(4), 46.
【16】Chen M Y, Bai P C, Zhang A F, et al. Materials Reports, 2015, 29(20), 105 (in Chinese). 陳夢洋, 白樸存, 張安峰, 等.材料導報 , 2015, 29(20), 105.
【17】Vilaro T, Colin C, Bartout J D, et al. Materials Science and Engineering: A, 2012, 534, 446.
【18】Chen X J, Zhao G R, Dong D D, et al. Chinese Journal of Lasers, 2019,46(12), 1202002(in Chinese). 陳秀娟, 趙國瑞, 董東東, 等.中國激光 , 2019, 46(12), 1202002.
【19】Choi J P, Shin G H, Yang S, et al. Powder Technology, 2017, 310, 60.
【20】Zuo W, Zhang Q M, Wu W J, et al. Journal of Rocket Propulsion, 2017,43(1), 55 (in Chinese). 左蔚, 張權明, 吳文杰, 等.火箭推進 , 2017, 43(1), 55.
【21】Lin X, Yang H O, Chen J, et al. Acta Metallurgica Sinica, 2006, 42(4), 361(in Chinese). 林鑫, 楊海歐, 陳靜, 等.金屬學報 , 2006, 42(4), 361.
【22】 Lv H , Yang Z B, Wang X, et al. Chinese Journal of Lasers, 2018, 45
(10), 1002003(in Chinese). 呂豪, 楊志斌, 王鑫, 等.中國激光 , 2018, 45(10), 1002003.
【23】Chlebus E, Gruber K, Kuznicka B, et al. Materials Science and Engi?neering: A, 2015, 639 (15), 647.
【24】Brynk T, Pakiela Z,Ludwichowska K. Materials Science and Engineering: A, 2017, 698, 289.
【25】Tomus D, Yang T, Rometsch P A, et al. Materials Science and Enginee?ring: A, 2016, 667 (14), 42.
【26】Li Y L, Lei L M, Hou H P, et al. Journal of Materials Engineering,2019, 47(5), 100 (in Chinese). 李雅莉, 雷力明, 侯慧鵬, 等.材料工程 , 2019, 47(5), 100.
【27】Deng X Y, Lu S Q, Wang Y C, et al. Special Casting & Nonferrous Al?loys, 2017, 37(8), 878 (in Chinese). 鄧曉陽, 魯世強, Wang Yachao, 等.特種鑄造及有色合金 , 2017, 37
(8), 878.
【28】 Huang W P, Yu H C, Yin J , et al. Acta Metallurgica Sinica, 2016, 52(9), 1089 (in Chinese). 黃文普, 喻寒琛, 殷杰,等.金屬學報 , 2016, 52(9), 1089.
【29】Graybill B, Li M, Malawey D, et al. In: ASME 2018 13th InternationalManufacturing Science and Engineering Conference, 2018, pp. 1.
【30】Zhao W W, Lin X, Liu F C, et al. Chinese Journal of Lasers, 2009, 36(12), 3220 (in Chinese). 趙衛衛, 林鑫, 劉奮成,等.中國激光 , 2009, 36(12), 3220.
【31】 Pang X T, Cheng X, Tian X J, et al. Rare Metal Materials and Enginee?ring, 2019(5), 1615(in Chinese). 龐小通, 程序, 田象軍, 等.稀有金屬材料與工程 , 2019(5), 1615.
【32】Liu K, Wang R, Qi H, et al. Physical Testing and Chemical Analysis(Part A:Physical Testing), 2019, 55(1), 15(in Chinese). 劉凱, 王榮, 祁海, 等.理化檢驗:物理分冊 , 2019, 55(1), 15.
【33】Zuo W, Zhang Q M, Lei Y, et al. Journal of Rocket Propulsion, 2017,43(3), 53 (in Chinese). 左蔚, 張權明, 雷玥, 等.火箭推進 , 2017, 43(3), 53.
【34】Yao Y S, Wang J, Chen Q B, et al. Laser & Optoelectronics Progress,2019, 56(10), 45 (in Chinese). 姚燕生, 汪俊, 陳慶波, 等.激光與光電子學進展 , 2019, 56(10),
45.
【35】 Du C, Zhang J, Lian Y, et al. Surface Technology, 2019, 48(1), 200(in Chinese). 杜暢, 張津, 連勇, 等.表面技術 , 2019, 48(1), 200.
【36】 Moat R J, Pinkerton A J, Li L, et al. Materials Science and Engineering: A, 2011, 528(6), 2288.
【37】Parimi L L, Attallah M M, Gebelin J, et al. Superalloys 2012, 2012,509.
【38】Klingbeil N W, Beuth J L, Chin R, et al. International Journal of Me?chanical Sciences, 2002, 44(1), 57.
【39】Prabhakar P, Sames W J, Dehoff R, et al. Additive Manufacturing,2015, 7, 83.
【40】Bi Z N, Qin H L, Dong Z G, et al. Acta Metallurgica Sinica, 2019, 55(9), 1160 (in Chinese). 畢中南, 秦海龍, 董志國, 等.金屬學報 , 2019, 55(9), 1160.
【41】Zhang J, Li S, Wei Q S, et al. Chinese Journal of Rare Metals, 2015, 39(11), 961 (in Chinese). 張潔, 李帥, 魏青松, 等.稀有金屬 , 2015, 39(11), 961.
【42】Vrancken B, Cain V, Knutsen R, et al. Scripta Materialia, 2014, 87(1), 29.
【43】Yang Q Y, Wu Y D, Sha F. Materials for Mechanical Engineering,2016, 40(6), 83 (in Chinese). 楊啟云, 吳玉道, 沙菲.機械工程材料 , 2016, 40(6), 83.
【44】Ahsan M N, Pinkerton A J, Moat R J, et al. Materials Science and Engi?neering: A, 2011, 528 (25?26), 7648.
【45】Shi Q, Gu D, Xia M, et al. Optics & Laser Technology, 2016, 84, 9.
【46】 Yuan X B, Wei Q S, Wen S F, et al. Hot Working Technology, 2014, 43(4), 91(in Chinese). 袁學兵, 魏青松, 文世峰, 等.熱加工工藝 , 2014, 43(4), 91.
【47】Li Y, Qi H, Hou H, et al. Materials and structural engineering (IC?MMSE 2017), Atlantis Press, 2017.
【48】Carter L N, Martin C, Withers P J, et al. Journal of Alloys and Com?pounds, 2014, 615, 338.
【49】Amato K N, Gaytan S M, Murr L E, et al. Acta Materialia, 2012, 60(5), 2229.
【50】Parimi L L, Ravi G A, Clark D, et al. Attallah, Materials Characteriza?tion, 2014, 89, 102.
相關鏈接